Corrosion protection: Taking effective measures against corrosive gases
Corrosion poses a constant threat to industry, leading to significant economic losses, safety risks, and declines in efficiency due to the decomposition of materials caused by chemical reactions with the environment. Corrosive agents such as sulphur dioxide (SO2), hydrogen sulphide (H2S), nitrogen dioxide (NO2), chlorine (Cl2), and other acid gases are particularly problematic. A highly effective method to combat and control industrial corrosion is molecular air filtration, especially when using impregnated activated carbon as a filter medium. This technology enables companies to reliably filter corrosive gases in order to prevent corrosion and maintain safe and successful operations.
Preventing corrosion: The crucial role of molecular air filtration
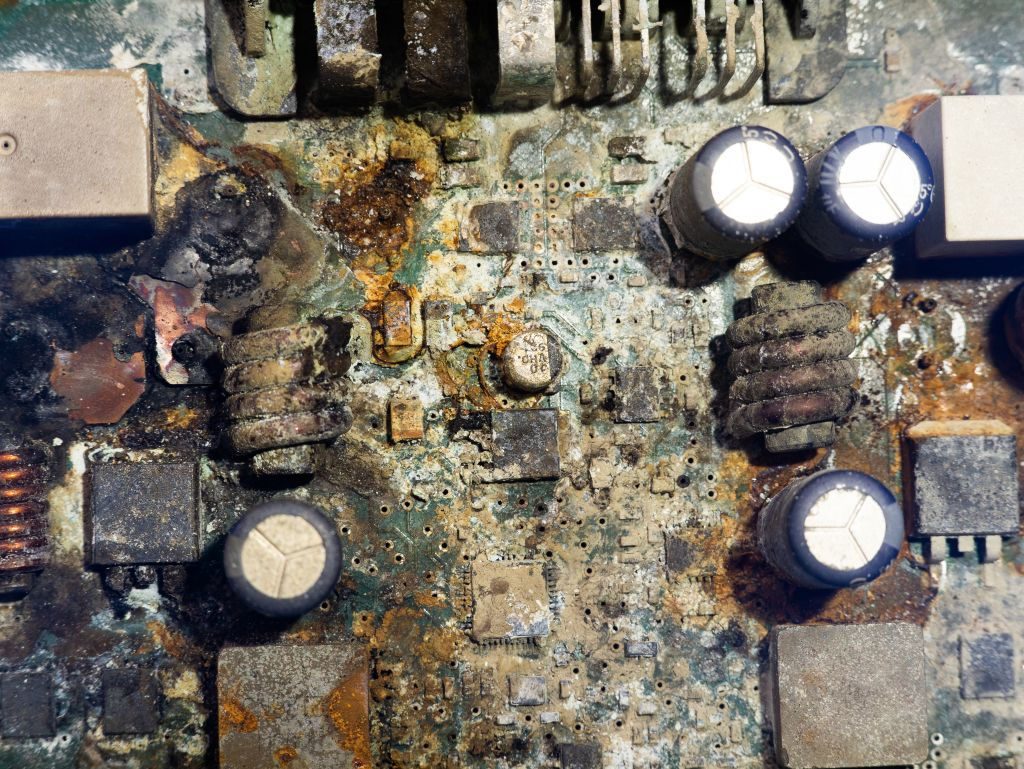
The issue of corrosion and its prevention rarely receives the attention it deserves. While highly corrosive industries, such as oil and gas, have long been vigilant when it comes to corrosion protection, many other sectors still underestimate the challenge. Chemical corrosion, especially in pipelines, metals, and electronic equipment, can cause machine failures, personal injuries, and substantial economic losses, damaging a company's reputation. Beyond traditional active and passive corrosion protection measures such as corrosion inhibitors or cathodic protection, the adsorption of harmful corrosive gases by high-performance air filters is vital.
Corrosive substances release gases like nitrogen dioxide (NO2) and hydrogen fluoride (HF), which threaten electronic and electrical control systems. Sulphur-containing gases, including sulphur dioxide (SO2), sulphur trioxide (SO3), and hydrogen sulphide (H2S), can cause severe corrosive damage. Molecular air filtration, however, helps effectively adsorb these and other corrosive gases from the air before they contact materials and cause damage. At MANN+HUMMEL, we use highly effective, specially impregnated activated carbon at the heart of this technology.
Impregnated activated carbon against corrosion damage
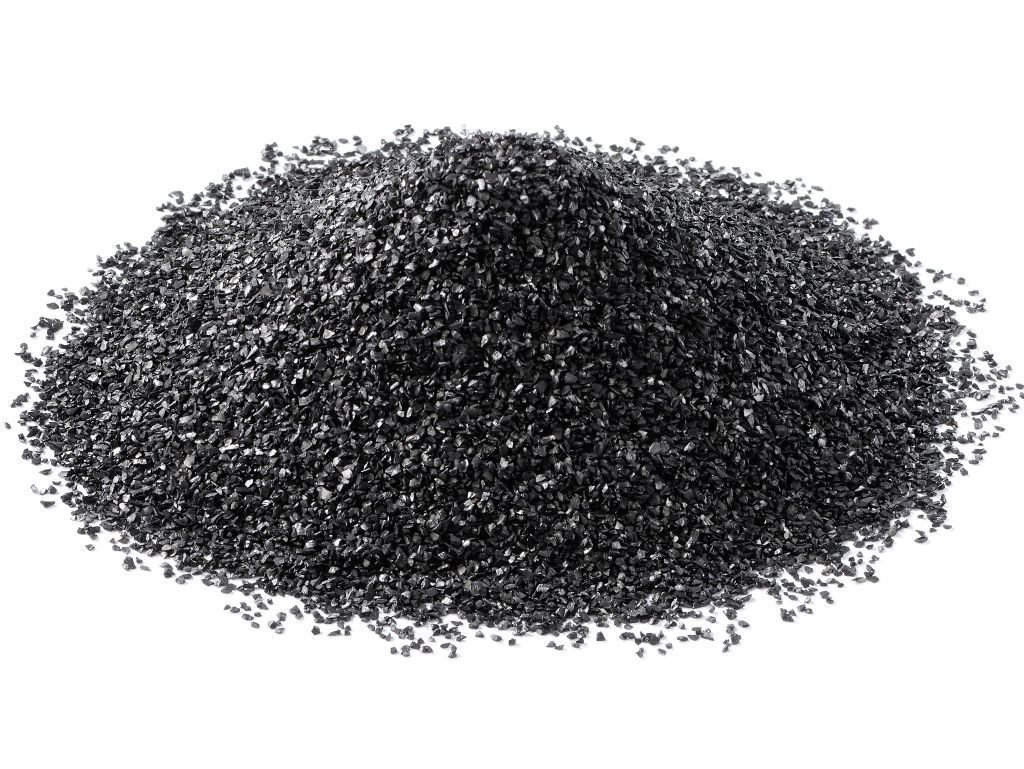
Activated carbon is ideal for corrosion protection due to its high adsorption capacity and unrivalled ability to successfully bind a wide range of organic and inorganic gases. Its effectiveness can be further enhanced by impregnating it against specific corrosive chemicals.
There are different approaches to optimise the effectiveness of corrosion protection systems using impregnated activated carbon:
By combining these approaches, the effectiveness of corrosion protection with impregnated activated carbon can be continually improved. However, the selection of the right adsorption material and level of impregnation depends on the specific corrosive gases to be addressed. That’s why we help our customers with identifying the optimal solution for their specific applications.
Corrosion protection with MANN+HUMMEL: Fully customised solutions for every industry
For over 80 years, we’ve been safeguarding industries with our customised molecular air filters that protect plants, infrastructures, people, and machines.
For inquiries about specific applications and potential solutions, the MANN+HUMMEL team is here to help you. Contact us today to discover how we can help support your corrosion management strategy.
Contact us
At MANN+HUMMEL, we’re here to support your air filtration needs! Whether you have questions about our products or need tailored solutions, our expert team is ready to assist you. Reach out to us via email, telephone or contact form to discuss your requirements, and let’s work together to enhance your air quality. Contact us today and experience exceptional service tailored to your business!